On August 16, 2016, Carbon (Carbon3D, Inc) today announced the addition of a leading 3D printing service bureau and contract manufacturer to its customer portfolio. Dinsmore Inc. will now offer their customers access to Carbon’s M1 printer and Continuous Liquid Interface Production (CLIP) technology. With CLIP, Dinsmore’s range of customers – from automotive and aerospace, to consumer and medical – are now able to produce polymeric parts that have the resolution, surface finish and mechanical properties required for both functional prototyping and final production.
"At Carbon, we’re working hard to deliver CLIP into the hands of the engineers and designers who will transform industries. With access to the M1, these leading service bureaus can better serve their innovative customers, and make a real impact in a number of industries. They are key partners on our journey to disrupt the manufacturing landscape."
Joseph DeSimone, CEO and co-Founder of Carbon
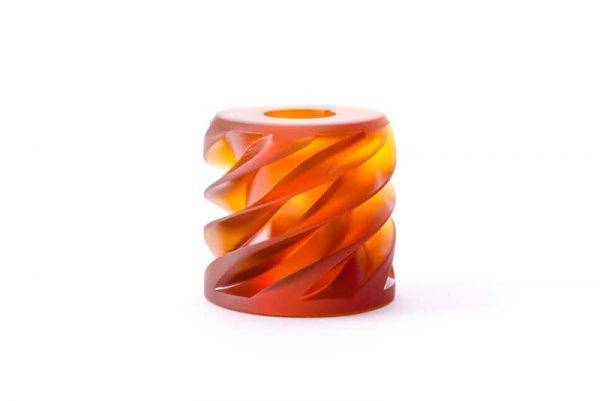
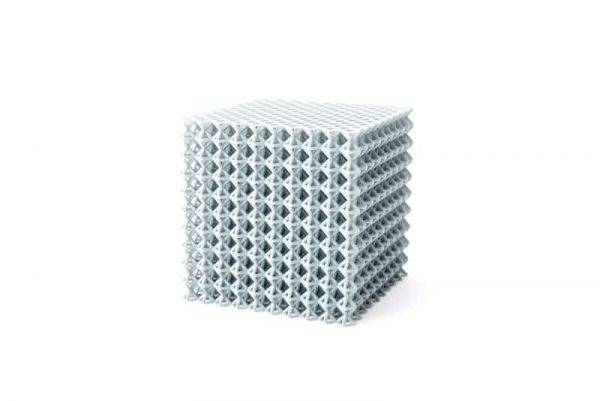
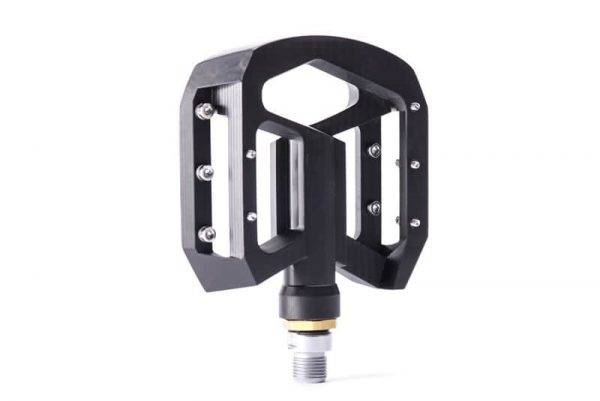
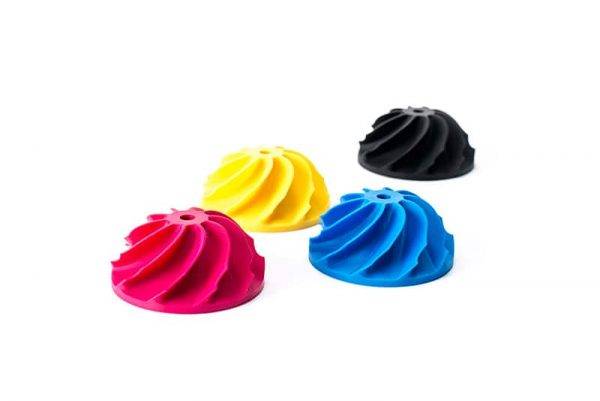
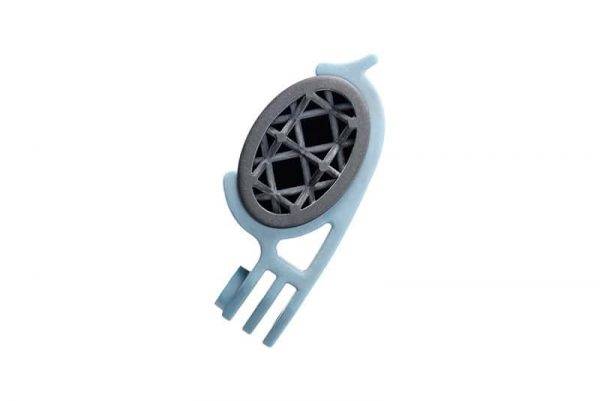
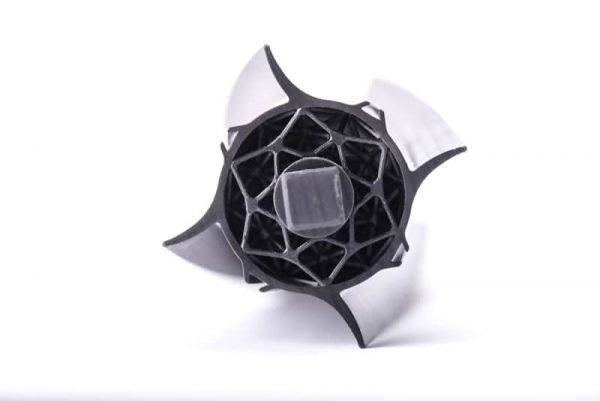
Materials
CLIP enables 3D printing with novel classes of polymers, including complex chemistries such as polyurethane and cyanate ester-based resins. The result is a diverse and growing selection of materials reflecting common engineering requirements.
- RPU (Rigid Polyurethane): Tough + abrasion resistant, stiff
- FPU (Flexible Polyurethane): Tough, impact + abrasion resistant, moderate stiffness
- EPU (Elastomeric Polyurethane): Highly elastic, resilient
- CE (Cyanate Ester): High temperature resistance, strength + stiffness
- PR (Prototyping): General purpose
Process
Traditional approaches to additive manufacturing are inconsistent. Their mechanical properties vary depending on the direction the parts were printed which depends on the layer-by-layer approach. With CLIP, the result is more like injection-molded parts with consistent and predictable mechanical properties. Parts created with CLIP are solid on the inside.
Benefits
CLIP parts behave consistently in all direction. The resolution and gentleness of the process make it possible to exploit a range of materials that have the surface finish and detail needed for end-use parts.
"The future of additive manufacturing lies in the ability to produce end-use parts. Carbon’s offering is truly innovative because of the range of materials we can print with, the quality of parts that come off the M1 machine, and the speed at which we can achieve the desired end-use results."
Jay Dinsmore, CEO and President of Dinsmore Inc

The M1 is a powerful new tool for product design and manufacturing. For the first time, it’s possible to 3D print isotropic parts with mechanical properties and surface finish like injection-molded plastics. No other additive technology delivers the synthesis of fit, form, and function needed to bridge the gap between prototyping and manufacturing. The M1 leverages a range of materials which are designed to meet engineering requirements — from the elongation and resilience expected of an injection molded polyurethane elastomer, to the temperature resistance of a glass-filled Nylon, and many more. Carbon currently offers five commercially available resin families.
Since unveiling CLIP in March 2015 and launching the M1 printer in April 2016, Carbon has set forth a bold vision to accelerate and reshape the future of manufacturing by introducing the world to the possibilities of a future fabricated with light.
About Dinsmore Inc.
Founded in 2002, Dinsmore & Associates is a single source provider of Design & Engineering, 3-D Printing, Additive Manufacturing, CNC Machining, and Injection Molding services. The Dinsmore team of industrial, electrical and mechanical engineers boasts twenty four years of experience with 3-D printing technology. They are committed to supporting customers throughout the product design and production journey. Dinsmore & Associates’ ultimate goal is a simple one: get customers to market FAST! For more information please visit Dinsmoreinc.com or follow Dinsmore on Twitter @Dinsmore_Asso.
About Carbon
Carbon is working at the intersection of hardware, software and molecular science to deliver on the promise of 3D printing, enabling creators to think beyond the limitations of convention to design the parts and products that will drive the businesses of the future. Carbon’s Continuous Liquid Interface Production technology (CLIP) was introduced simultaneously at TED 2015 and to the scientific community on the cover of Science Magazine (Science, March 2015). In April 2016, Carbon introduced the M1, its first commercial CLIP-based additive manufacturing machine, created as a comprehensive solution for the next era of design and manufacturing. To date Carbon has received $141 Million in funding. For more information please visit Carbon3D.com or follow Carbon on Twitter @Carbon3D.